Master's of Science: Aerospace Engineering (12/2017)
Bachelors of Science: Aerospace Systems Engineering
Minor(s):Physics and Applied Mathematics
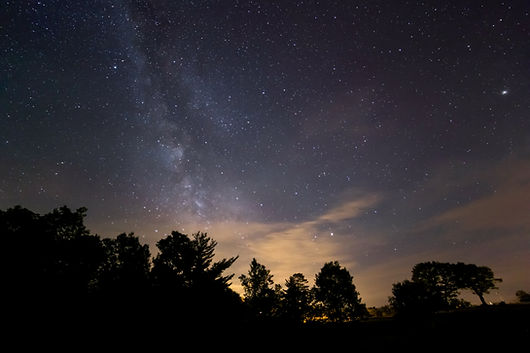
-
Materials and Structures Division in the High Temperature and Smart Alloys Branch
-
Tested a variety of materials and aerospace structures for research and engineering
-
Testing types include: Monotonic and biaxial tensile, fatigue life, creep, fatigue crack forth, thermomechanical fatigue and structural validation
-
Materials tested include: Metallic alloys and super alloys, ceramic matrix composites (CMCs), polymer matrix composites, additively manufactured metals and metal alloys, polyimide aerogels, polymers, and aluminum honeycomb composite sandwich structures.
-
Measured specimens precisely using a Projectron Comparator
-
Captured fractured surfaces using an Olympus SZH Zoom Stereo Microscope System
-
Trained in ARAMIS and TRITOP digital image correlation systems
-
Trained on MTS 858 and MTS 810 Material Test Systems, along with MTS and McGaw Test Controls Systems
NASA Glenn Research Center Cleveland, OH, 08/15-Pres.



-
Conducted a full modal study on what is known as the Jim Beam Structure
-
Created a full Finite Element Model of the Jim Beam Test Article in FEMAP
-
Used MSC-NASTRAN to obtain different modes, and Frequency Response Functions
-
-
Performed FEM mini-studies on different plate structures, element sizing, fastener types and stiffness
-
Conducted modal impact testing using the roving hammer technique on the Jim Beam structure
-
Tested different free-free boundary conditions (bungeed structure and structure on airbags)
-
Tested reciprocity and the linearity of the test structure
-
Used Pulse Laboratory and Brüel and Kjær Data acquisition System
-
-
Obtained modal parameters (Eigenvalues/Damping/Residues) through curve-fitting data in ME’Scope
-
Correlated test data to FEM data using Modal Assurance Criterion (MAC) Checks and updated FEM using FEMTools
NASA Kennedy Space Center Cape Canaveral, FL, 06/15-08/15




-
Game Changing Development (GCD) design project to return an Antares rocket second stage using a Hypersonic Inflatable Aerodynamic Decelerator (HIAD) (Main Focus-Deorbit propulsion and Flight Trajectory)
-
Performed Inflight vibration test and analysis to produce PSD curves for the following aircrafts: HU-25 Falcon Jet Aircraft and B200 Kings Air Propeller Aircraft
-
Conducted and assisted on modal test and analysis on both 3–meter and 6–meter HIAD models
-
Wrote LabVIEW code to aid in motor test and life testing data acquisition
-
Trained/executed material classification from running/analyzing Gas Chromatography–Mass Spectrometry (GC-MS)
-
Classification and contamination engineering for Stratospheric Aerosol and Gas Experiment (SAGE) III on ISS
-
Designed gaseous Nitrogen piping system throughout the Systems Integration and Test Branch building
NASA Langley Research Center Hampton, VA, 01/13-08/14



-
Founder/President/Advisor
-
Led a group of 60 students, 7-sub-systems, to successfully launch a sounding rocket to an altitude of 20,000 ft.
-
Used BurnSim and Open Rocket to simulate max dynamic pressure forces and propulsion burning characteristics
-
Performed ANSYS-Fluent simulation on different nosecone and fin designs
-
Currently advising the research sub-system in variable nosecone design and spin stabilization methods
-
Performed STEM outreach
-
Created budget proposals that successfully raised $35,000 in funding
-
Visit akronauts.wix.com/akronauts for updates
University of Akron's Rocket Design Team Akron, OH, 05/14-Pres.



University of Akron's IDEAS Tutor Akron, OH, 08/12-08/14
Tutor undergraduates in fundamental engineering courses
TA: Mechanics of Materials
LA: Dynamics, Statics, Mechanics of Materials
Tutor: Tools for ME, Dynamics, Engineering Analysis I-II, Thermodynamics I, Fluid Mechanics I, Basic Electrical Engineering, College Algebra, Calculus I-III, Differential Equations, College Physics I-II, University Physics I-II
